Inventory Control
Complete inventory management
system allows several costing methods, multiple
warehouse locations, lot tracking, and more.
Reports allow you to analyze and control your
stock. Complete link to Purchasing, Sales Orders,
Accounts Receivables, and General Ledger.
Integrates with kits and bill of materials.
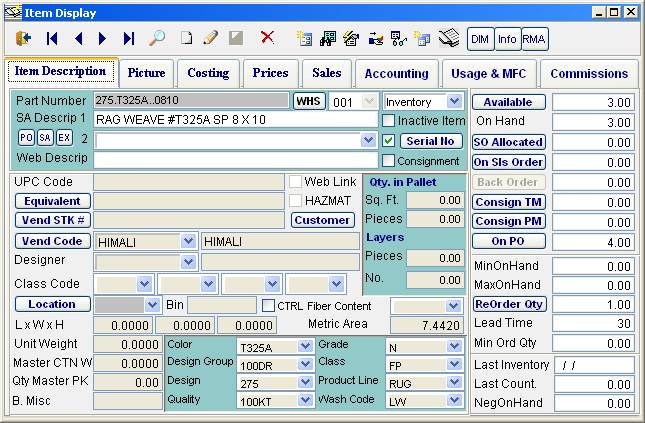
Inventory Master -
Item Description
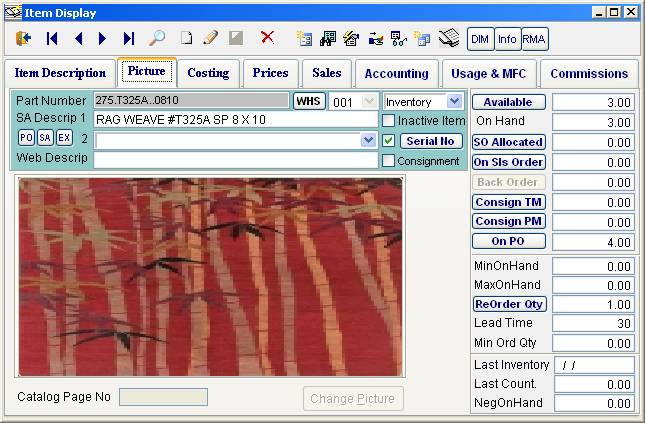
Inventory Master - Item Picture
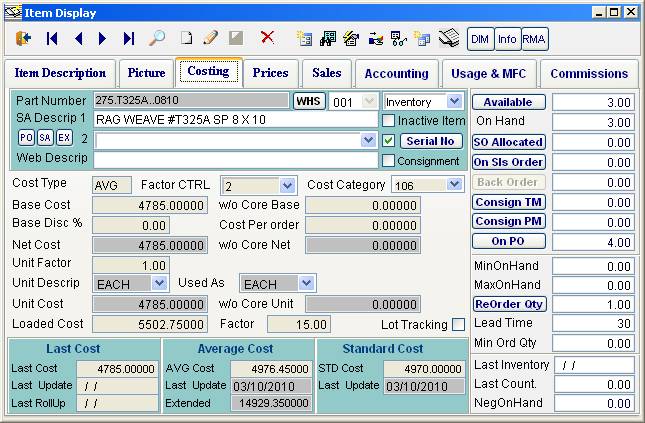
Inventory Master -
Item Costing
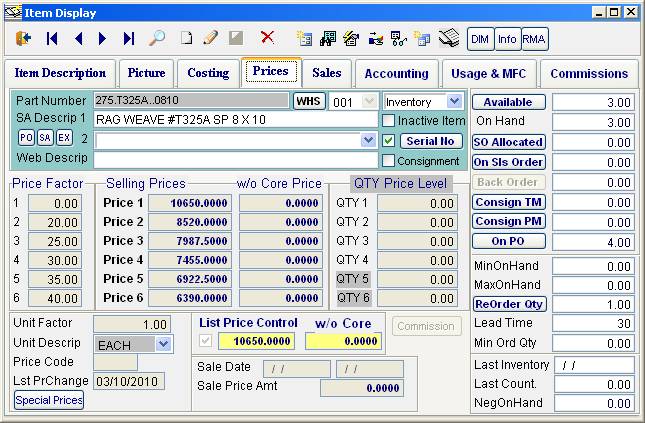
Inventory Master -
Item Prices
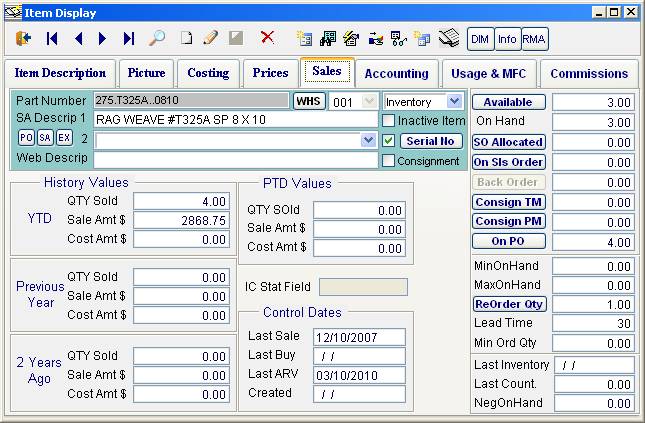
Inventory Master -
Item Sales
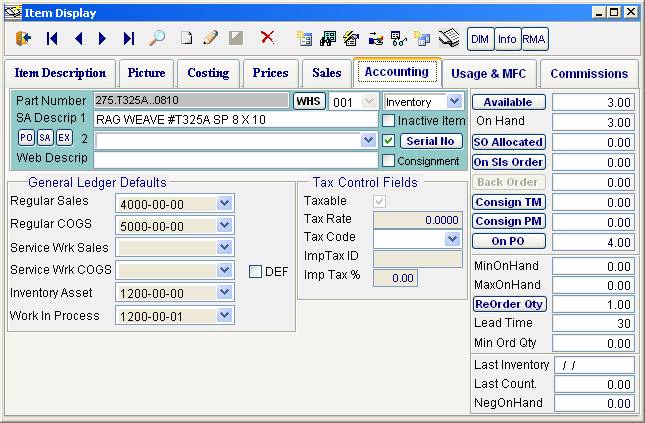
Inventory Master -
Item Accounting
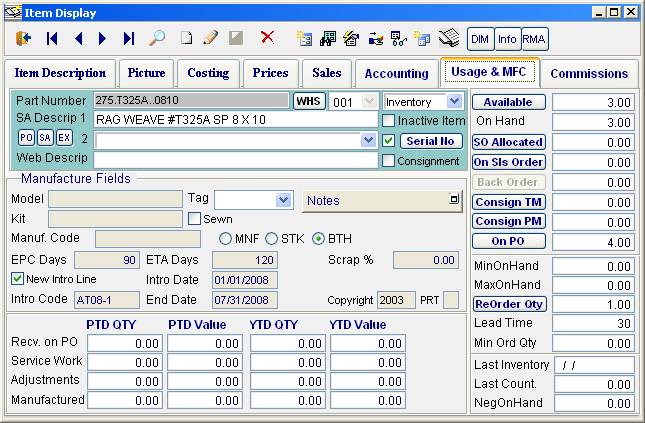
Inventory Master -
Item Usage and Manufacturing
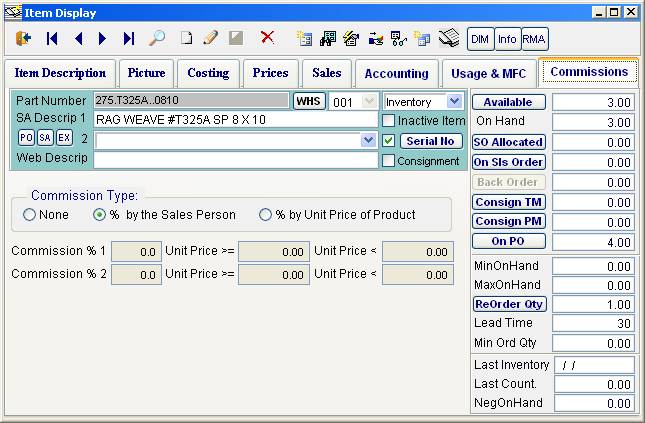
Inventory Master -
Item Commission
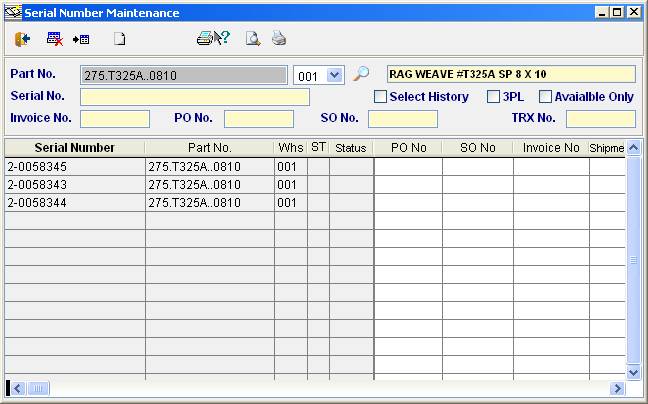
Inventory Master -
Serial Number Status
- Select one of four different cost
methods, Average, FIFO, LIFO, or Last Cost.
- Multiple warehouse locations
per item.
- Multiple locations within
each warehouse.
- Define units of measure for
purchasing and selling.
- Define each item with a Part
number, UPC code, unlimited vendor part
numbers, unlimited customer part
numbers, unlimited equivalent part numbers.
- Separate item description for
purchasing and sales.
- Each item has an extended
description with unlimited number of
characters.
- Unlimited bin locations per
item.
- Item types include:
Inventory, Non IC, Raw Material, Kit, Service,
and Component.
- Define unit of weight.
- Carton pack and qty per
carton.
- Item origin either from
stock, manufacture or both.
- Include picture of inventory
item on display screen.
- Each item can have multiple
price schedules. Can be defined by
customer, by markup from cost, by discount
from list price, by volume, by product code.
- Six price factors per
item. Calculate markup from cost or
markdown from list price.
- Six (6) quantity price level
for each item. Selling price determined
by quantity of item purchased.
- Customer specific price
control for each item.
- Each item can be assigned a
promotion price with expiration date.
- Allows for multiple vendors
for same part number.
- Classify each item by one
class code and up to three sub class codes.
- Master parts display shows
item status: Available, On Hand,
Committed-to-Ship, Committed, Back Ordered, On
Order, Min-On hand, Max-On-Hand, Re-Order
quantity, Minimum Order Quantity, Last Stock
count date, last physical count, negative
variance.
- Assign catalog page number
item appears in.
- User defined status field.
- Flexible unit cost
definition: Base cost, Discount percentage
from base cost, net cost, Unit factor, Unit
cost, landed cost, average cost.
- Allow each item to define tax
status, tax rate, tax code, import tax
percentage.
- Define GL link for each item:
Sales, Asset, Cost and Service GL account.
- Item master display screen
shows sales history: period-to-date,
year-to-date, previous year, two (2) years
ago. Both quantities sold and dollar
value. Displays last sale date, last buy date,
last arrival date, date item created.
- Query system by class code
and item type for fast on-line searches.
- Transaction processing system
that allows adjusting stock quantities,
warehouse transfer, or physical count
adjustments.
- Transaction processing links
to GL to adjust costs (inventory valuation).
- Basic bill of materials for
kits.
- Automatically deducts raw
material stock from kit items at time of kit creation.
- Complete lot tracking control
through item life cycle: purchase order,
sales order, to invoice.
- History look-up of lots by
entry number, invoice number, sales order
number.
- Allows for warehouse maintenance
function. Create up to 65,000 different
warehouse locations.
Reports
- General item listing report.
- Price labels.
- Items in stock report.
- Items out of stock report.
- Items on order report.
- Stock count work sheets report.
- Warehouse bin location report.
- Stock re-order report.
- Inventory adjustments report.
- Kit creation report.
- Inventory physical count report.
- Parts status report.
- Lot tracking control report.
- General Ledger Distribution report.
Lot
Tracking
The lot tracking system allows you
to assign a control number to your incoming
stock. This number follows the item through
the sales cycle and can be recalled from history.
- Assign lot numbers manually
or auto generate them.
- Lots can be assigned at time
of PO receipt or after the fact.
- Mark an item as bonded
inventory.
- Only "cleared"
items can be transferred into sellable stock.
- Track lots through sales
cycle into sales history.
- Reports
- Lots by item.
- Cleared items.
- Adjustment register by lots.
- Sales history by lot number.
Serial
Numbers
The Serial Number capabilities of
VFP allows tracking serial number from the PO
receipt to the final sales invoice.
- Alpha numerical serial number
field.
- Identify inventory items as
serialized or not.
- Assign serial numbers to
incoming stock during purchase order
receiving.
- Pick serial numbers during
order entry or invoicing.
- Serial number history lookup.
- Scan serial numbers during
sales and purchase processing.
- Reports
- List serial number for one
part number
- Select all serial number for
an invoice, sales order, purchase order or
inventory transaction..
Kits
The KIT functions allows for a
simple bill of material system. Create a
bill of material list for unlimited number of
items.
- Enter kit on fly.
- Assign unlimited number of
items to a kit.
- Allow sub kits to be
assigned.
- Automatic cost calculation
based on component count.
- Create an inventory
transaction to enter a kit into stock.
- Automatically adjust stock on
kit creation.
- Automatically adjust cost and
price for kits.
- Reports
- Bill of materials list by
item number.
- IC transaction register for
manufactured kits.
|